How do we put wind farms in the sea?
1st September 2017
Wind power has gone from strength to strength, becoming a popular source of renewable power.
As an energy source, it is limitless, and the continued growth of the industry has helped to push down the costs of developing wind installations.
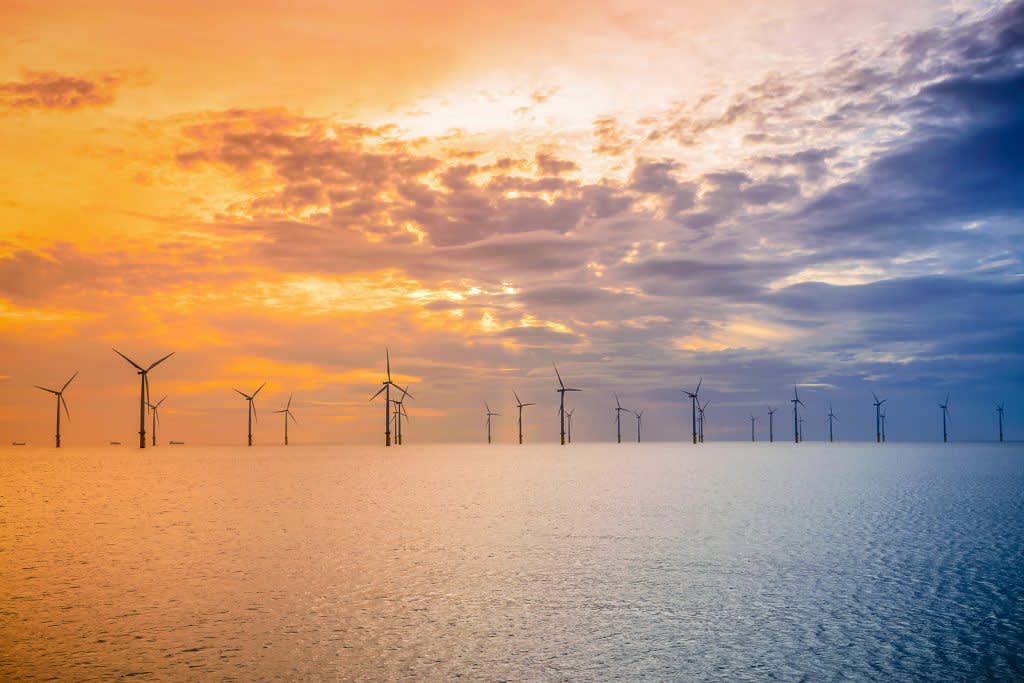
But how does a wind farm take shape? It’s a lengthy process, with several steps along the way from development and engineering to construction and, finally, operation.
Here, we take a detailed look at how wind farms are put together – both onshore and offshore.
Stage One
How do you decide where to put a wind turbine?
First of all, a site must be identified and the wind resource of the area – the potential energy contained in the wind – needs to be determined.
This measures the wind speed, temperature, pressure and humidity. At least one years’ worth of data must be collected to give an accurate indication of average wind speed.
Wind resource is dictated by a number of factors. Geographical and topographical features can affect the energy potential of wind, altering the speed and the kinetic energy available in it.
Onshore, there are more obstacles which alter the wind; at sea, wind speeds are higher and more consistent. This translates into greater energy production, which is helping offshore wind to grow in popularity.
However, moving turbines offshore creates new logistical and engineering challenges: offshore wind farms must be resilient to the harsh conditions at sea, including strong winds and choppy waters.
Stage Two
The construction process
The next stages are the design and the construction of the turbine. The design process is standardised; the choice of materials and model is consistent across wind farms.
As a result, the horizontal-axis wind turbine is the standard model, and the materials most commonly-used during construction are steel and fibreglass. These materials provide the perfect blend of qualities, offering strength and stability. Steel makes for a stable tower, while fibreglass is light enough to catch the wind, but firm enough to withstand high wind speeds.
While the turbine is being constructed, other work is underway to facilitate its installation. This includes preparing the foundations for the turbine to sit on, as well as connecting the export cable (or cables) which transports the generated electricity away from the site.
Stage Three
Building a fixed foundation
Onshore turbines sit on concrete foundations. Depending on a number of factors (such as soil quality, water retention by the soil, the weight and height of the turbine, and so on) the depth of the foundations can vary.
This helps to provide the stability needed for turbines, which are tall and experience stress from the force of the wind.
While these foundations are suitable at the moment, in the future it may be the case that foundations for onshore turbines need to take up less space while offering similar support.
For offshore turbines, foundations are slightly more complex; turbines are either fixed or – currently experimental – floating turbines. For fixed foundations, there are two options:
The first involves driving a single steel monopile into the sea bed. This single leg is suitable for supporting wind turbines in depths of up to 30 metres. The second uses a steel jacket structure – similar in shape to electricity pylons – which are suitable for depths of up to 50m.
In both cases, the structures are driven deep into the seabed. Monopiles can be up to six metres in diameter, with the wide foundation to support tall turbines. Steel jacket structures have four smaller legs, providing additional stability in deeper waters.
While fixed foundations are practical up to a water depth of about 50 metres, beyond this the costs begin to spiral and the process of fixing the foundations to the seabed becomes more difficult.
As a result, engineers are experimenting with floating foundations in deeper waters. These foundations could help to take offshore wind energy to water depths beyond 50m. The Hywind project in Scotland is currently trialling floating foundations at water depths up to 120m.
Building a floating foundation
Similarly to fixed foundations, there are a number of different floating platform designs.
There are three classifications: a semi-submersible platform, a spar-buoy system, and tension-leg platforms. In each case, the foundations are fixed to the seabed using tethers or anchors.
Semi-submersible platforms are buoyant structures which are anchored to the seabed; the weight of the wind turbine counteracts the buoyancy, giving the structure its stability.
A spar-buoy uses a cylindrical structure filled with ballast submerged below the surface of the water. The turbine fitted atop the structure is lighter than the weight of the ballast, which creates buoyancy.
Tension leg platforms (TLP) are semi-submersible structures which are anchored to seabed with tensioned mooring lines. TLP structures have already been proven by the petroleum industry, which has for years used floating rigs to access undersea oil and gas wells.
In any of the above instances, the turbine sits atop the floating foundation, and must be able to withstand hostile conditions. This places extra stress on the anchors and mooring lines. As such, the Hywind project (which uses spar-buoys) is important in demonstrating that floating platforms can be successfully used to support wind turbines. It has been proposed that a floating foundation for wind turbines could also accommodate a wave turbine, reducing intermittency and increasing total generation capability.
The International Renewable Energy Association (IRENA) has recognised the potential of floating foundations, listing the the advantages and disadvantages of each of the above types of platforms in their Floating Foundations report (this link will open in a new tab).
Stage Four
Putting the pieces together
Once all of this (literal and figurative) groundwork has been done, the turbine is ready for construction. The turbine blades and tower need to be transported to site where they are assembled, before undergoing testing.
Once the foundations are complete, the component parts of on onshore turbine are put together over the course of a few days. This takes at least two cranes, with one lifting and the other stabilising the airborne parts.
First the tower is erected, then the nacelle – which houses the generator and other moving parts of the turbine – is fitted to the top. The blades are then individually attached to the hub before it is lifted up and attached to the nacelle.
Offshore construction requires more logistical manoeuvring, however. The turbine must be transported by ship to the site and assembled piece by piece.
This requires specialist ships designed to carry heavy loads, as well as cranes to hoist the parts into place. Working at sea makes this a more challenging process, but the same steps are followed.
When the construction process is complete, the turbine undergoes testing to ensure that everything is operating as it should. After testing, the turbine is ready to generate electricity and feed it into the grid.
In short, it’s a lot of work – now imagine how much that work multiples when you’re building a wind turbine larger than Blackpool Tower…